so fun fact inhaling yummy iron dust is not very BASED.
and i mean i could wear a respirator, but the whole thing is even with wearing some safety's and a respirator i still got iron dust in my eyes, and have had about 4 eye infections. so last weekend i decided to fix that, i took a Hepa filter and laser cut a mount for a delta server fan and made 2 rings which hold the filter via caughter pins, i also had a mic arm that i lost the end. It sucks up all the iron dust from polishing. And if your wondering i really have only been at this die shop for a few months (basically 1 month after i started this form.) and Ive had a lot of challenges with working at this establishment, at least job wise. the people that i work with are really nice and have never had any problems. but the jobs are shitty to say the least and pay is not that good. im technically a maintenance worker, but i end up doing all the "shitty jobs" and i really dont get paid that much, im part time and get paid $14.60 hourly which a walmart worker gets paid $14 from where i live. and i really have a passion for machining, my senior year i took a machining class, and i was hooked.
all i really do is cut, size and polish dies and other junk like running the cnc (which i am a legit a button pusher) i know a little gcode like g73 is a peck drill can cycle. but i dont get to program or anything, i just take parts of of the vice and put new ones in and press cycle start
the shitty part is that for a lot of local shop you needed to know how to run a CNC. and sadly the class i took was a 2 year course and the second year was learning CNC, so i never got to.
and that left me to finding a job that i could be hired and hopefully work my way up. at this point i don't think im ever going to get a promotion, and am currently searching for a new job. i know this is rather personal, but what do you guys think?
ive been on the fence about leaving, and some of you may be wondering why i made the filter, and its because its kinda the whole fuck around and find out thats at my work place. if a worker asks for something like new ppe, the boss dislikes you and you basically get punished in a way, shittier jobs, less hours, denied days off.
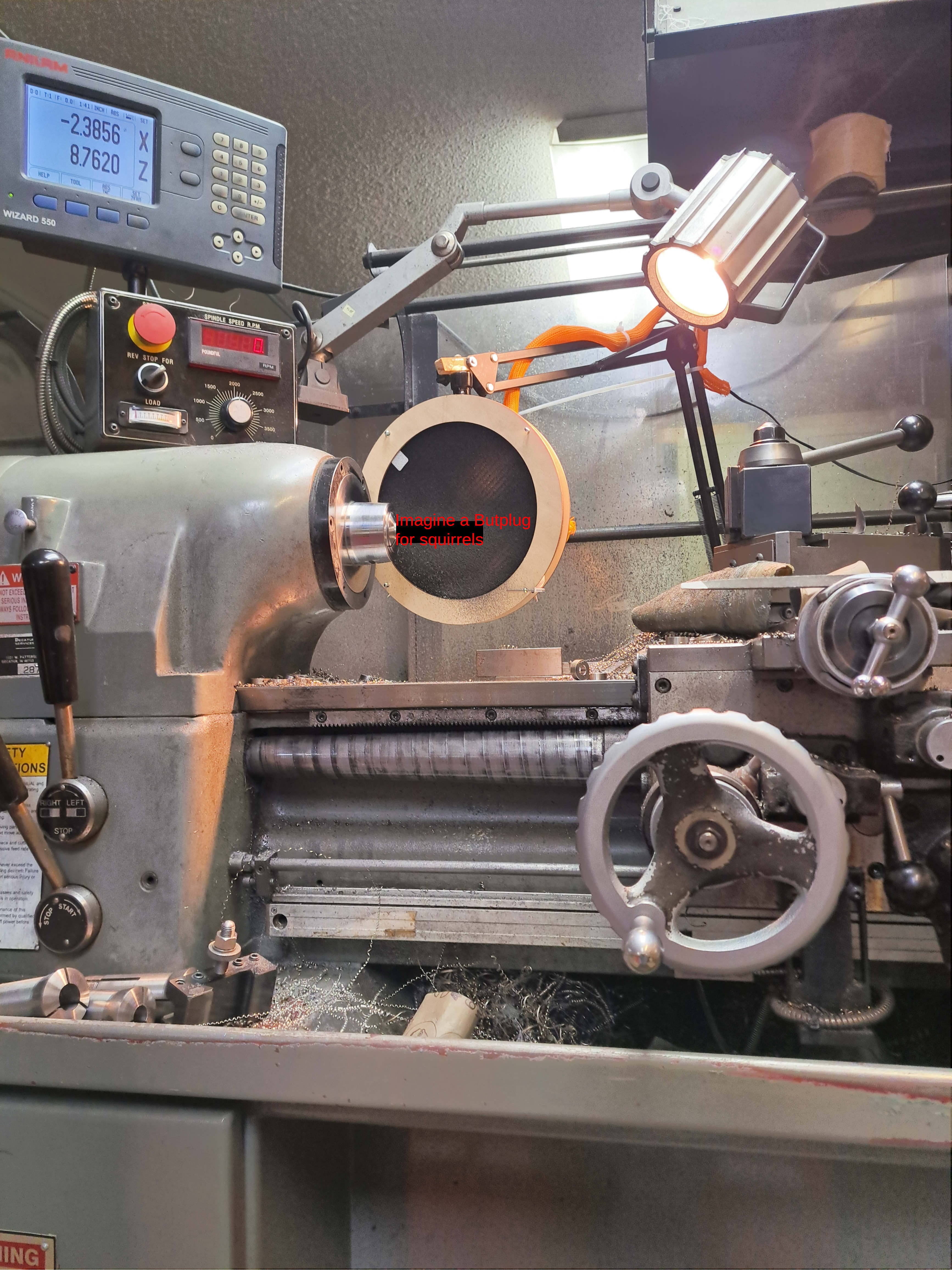